Contractor Auditing
Most organisations have a need to work with contractors. Some of which will be engaged to undertake specialist work on a regular basis know as reactive or Pre-Planned Maintenance (PPM).
Reactive Maintenance & RepairsContractors, particularly those working on a reactive basis , often find themselves in unfamiliar surroundings which may contain hazards such as, working at height, high voltage, asbestos, chemicals and extreme noise and temperatures. If care is not taken to ensure the correct health and safety procedures are in place, and followed. the contractor activities may lead to an increased level of risk not only to the contractors themselves but also to employees, subcontractors and any members of the public that they may come into contact with on site.
PPM Tasks
PPM tasks are derived form an industry recognised maintenance regime call SFG20. All PPM tasks should be surveyed with a full and detailed set of Risk Assessment Method Statement (RAMS) associated to every individual task with a copy of this document placed int he site folder along with an annual Planner of the PPM activities.
Job sheets should be completed in full with any defects followed through to quotation.
Below are typical elements of building plant that require regular PPM tasks;
- Boilers
- Pressurisation Units
- Air Conditioning
- Chillers
- Cooling Towers
- Water Heaters
- Pumps
- Booster Pumps
- Lifts
- Refuge Systems
- Fire Alarm
- Fire Extinguishers
- Access Control
- CCTV
- Lightening Protection
- Emergency Lighting Protection (Monthly & Annual)
- Air Handling Units
- Ventilation Systems
What are my legal duties and obligations when using a specialist contractor?
As an agent or a person in control, you must consider contractors’ health and safety arrangements. It is a requirement of current legislation including the Health and Safety at Work Act 1974, Management of Health and Safety at Work Regulations and the CDM Regulations that organisations establish the competence, in terms of the health and safety arrangements, of all contractors who carry out regular work for their company whether this is at their own offices or at any of the premises or sites they manage on their clients behalf.
When ever any repairs are being carried out, a full and detailed set of specific Risk Assessment Method Statement (RAMS) should be requested and the relevant Permit to access or Permit to Work should be issued, and recorded.
Clients and contractors also have special responsibilities under the health and safety regulations for dealing with special hazards such as chemicals and asbestos.
Selecting Competent Contractors
When you appoint a contractor you need to ensure they have the ability to carry out the contract to the desired standard without causing any risks to health and safety. It is good practice to develop a defined list of appropriate selection criteria which can be used to help evaluate a contractor.
A contractor appraisal form is often used to help with this process. As part of the evaluation process you may wish to request certain pieces of documentation including evidence and details as;
- Work experience in a similar field/project
- Qualifications & skills
- Accreditation's
- References
- Training particularly health and safety training
- Risk assessments and method statements for the work to be carried out
- Accident & reports
- Financial status
At 1968 Compliance, we are able to assist you in choosing the right contractor for the job in hand therefore it is imperative to ensure your chosen contractor has one or all of the below accreditation;
- REFCOM
Certificated
- FGAS Certificated
- Gas Safe Register
- Safe Contractor Approved
- Contractor Plus Certificated
- Environment Agency Waste Carrier
- SSAIB Certificated (Security Systems and Alarms Inspection Board)
- UKAS
Certificated
(UK Accredited Scheme)
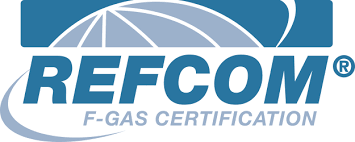
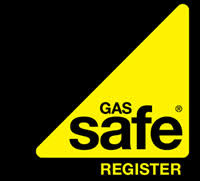
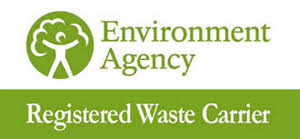
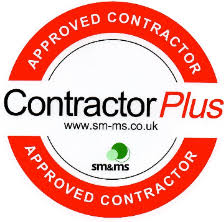
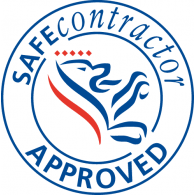
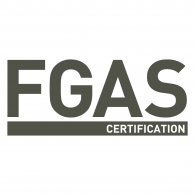
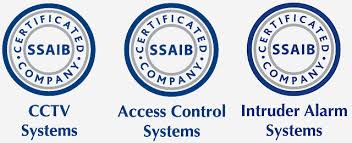
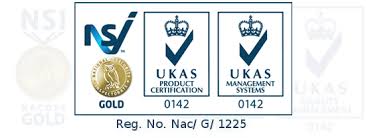